How Heavy Industrial Metal Fabrication Is Done?
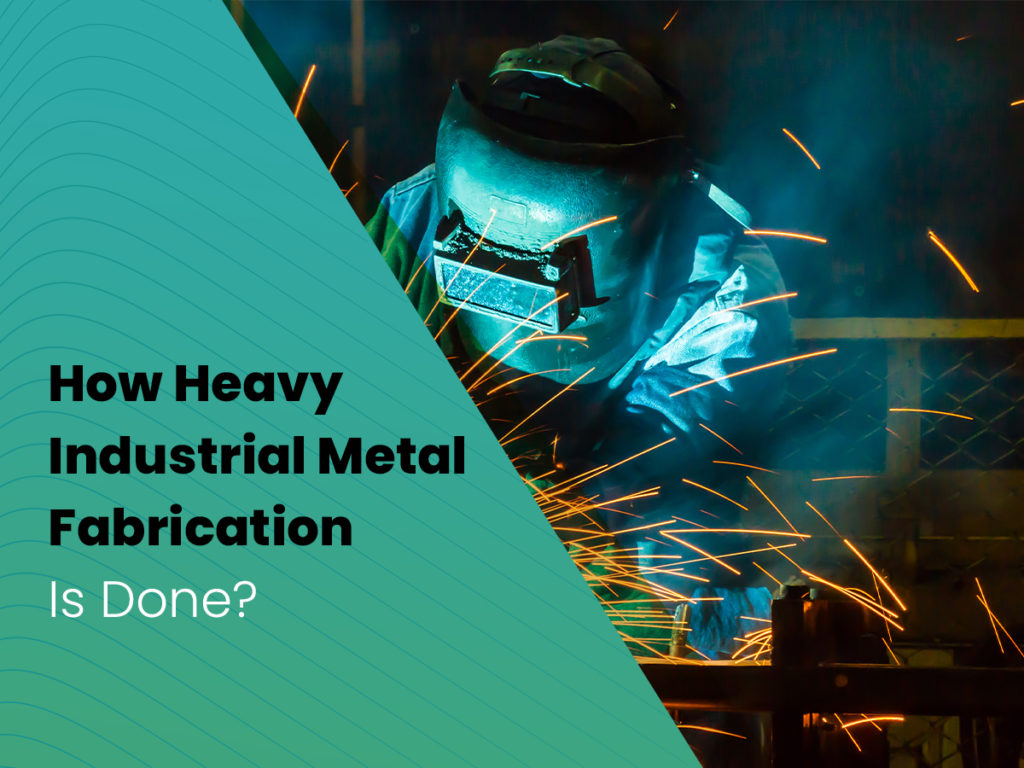
What is metal fabrication?
Making mechanical or structural components out of metal scraps is referred to as “metal fabrication.” The process entails cutting, welding, machining, shaping, and assembling for the final result. From handrails to large gear and equipment, metal fabrication projects are all over. Cutting and hand tools; architectural and structural metals; hardware manufacturing; spring and wire manufacturing; screw, nut, and bolt production; and forging and stamping are only a few of the subsectors that fall under this category.
Centralization of these various processes, which are often required to be conducted concurrently, is the primary value of metal fabrication factories. A one-stop metal fabrication facility reduces the need for contractors to work with several suppliers to accomplish complex projects.
Many industries and consumer products benefit from the metal fabrication industry’s wide range of applications. Plate metal, fittings, castings, formed and expanded metal, sectional metal, flat metal, and welding wire are among the most commonly used raw materials. Work with these raw materials and their ultimate products is performed by a wide range of specialists in the shops, including welders, ironworkers, blacksmiths, boilermakers, etc.
Application of fabrication process.
Mining, construction, manufacturing, shipbuilding, automotive, aerospace, and energy sectors all employ metal fabrication in some capacity.
· Construction
Steel and fabricated steel items are the material of choice for most architects and engineers. Metal fabricators can produce many metal sections to make the basic structure of projects such as bridges, warehouses, skyscrapers, and other large-scale structures. Metal fabrication has become an essential part of the construction sector.
· Aerospace
In the field of aerospace engineering, you can work on anything from commercial jets to advanced military planes for Canada’s armed forces. Metal fabrication is used to make these planes. Metal components are manufactured, assembled, and integrated during the manufacturing process. Manufacturing spaceships require the use of metal fabrication.
· Energy
Companies in the oil and gas industry, wind farms, nuclear power plants, and solar power plants all utilize metal manufacturing. For example, in these industries, the goods employed include wellhead and platform structures for oil and gas extraction, pipeline components for electricity generation and transmission, and wind turbine and transmission tower components. Metal fabrication is used to make all of these things.
· Mining
The mining sector relies heavily on steel because it is a byproduct of mining. On the other hand, mining itself necessitates a large number of metal fabrication-made machines and tools. Draglines, trucks, loaders, and shovels are just some of the mining equipment you’ll come across on the job. Fabricated steel sections are used to produce all of the above equipment. Rails, beams, rods, grates, pipes, and fittings are some of the steel parts found in mining.
· Ship Building
Metal fabrication items are widely used in a variety of shipbuilding equipment. Steel flooring and grating, ladders, steel sheets for hulls, conveyance tubing, stairs, and platforms are some of the industry’s most popular goods. Ships and the military both use metal fabrication for repairs and upkeep.
Key Elements of Quality Fabrication Work:
Custom fabrication procedures that yield high-quality creations with long-term worth are shown in the following instances.
Setting Design Intent
The metal fabrication design is critical for the desired result to be achieved, which is added value. What’s the point of making this up? Maybe it’s an industrial option to have two oil tanks with multiple entry points on the roof? Or do you have anything else?
A full-service fabricator can take a typical industrial plant or an engineering blueprint and create a precise design that will meet the needs of even the most difficult fabrications. This may necessitate further refinement and testing of the invention by industry-specific criteria or regulations, as well as the identification of all the necessary components for the project’s final construction.
Custom metal fabrications, such as the following:
· As well as silos and hoppers that can be used for dry solids metering or other material handling functions for feed and grain tanks.
· It’s possible to boil the syrup to keep it liquid while storing it in this type of container.
· Storage units can be accessed from various heights using custom spiral staircases with cross-over platforms.
MTC Shape Cutting, Pro Nest, or AutoCad files may be used to start a custom fabrication or even a hand-drawn blueprint. Engineering skills can help ensure that a project’s value-added specifications are met before the copy even starts.
Metal Cutting & Forming
The metal fabricator must first determine which procedure is best for the metal’s type and thickness before starting any cutting. Laser cutting can be used for delicate metal fabrications and large steel plates that need to be precise. Because of the possibility of spray reactions or surface flaws, lasers are not recommended for use with metal composites or materials that contain impurities.
Plasma machines equipped with Computer Numerical Control (CNC) can give outstanding precision in creating complicated steel metal forms. Plasma tables are frequently employed to machine intricate shapes or holes in thick metal plates using a plasma torch.
When working with structural steel, sawing is a better option because massive beams are needed for the final production. Plate shears are the most cost-effective solution for cutting simple designs, and these shears are better suited for carbon steel ductwork or long-lasting metal bins.
Bending, plate, and angle rolling, or punching may be required to shape the metal. For the best results, the correct equipment must be used.
Metal forming machinery may include:
· Hydraulic press brakes, both mechanical and CNC.
· Plate rolling and angle rolling machines are included.
· Punching machines that use beams and computer-controlled machining centers.
· Multi-function ironworkers that may be used for slicing, punching, and bending
Metal forming success relies on selecting the right machinery to execute the work, whether it’s thick carbon-steel plates or copper filigree. A full-service metal fabricator will generally have all of the above equipment on hand to save both time and money.
Custom Welding & Assembling
Using custom welding and assembly procedures, metal fabrications can be made to match industrial requirements. With certified welders and a documented quality control program (QC), custom fabricators are more likely to meet industry standards that offer value.
Ask for proof of welding certifications before collaborating with a metal fabrication firm. Included in these credentials are:
· Complying with the Canadian Welding Bureau (CWB) requirements.
· A Welding Procedure Specification (WPS) following ASME Section 9 and API-650 welding practices
· Certified by the American Welding Society (AWS) to weld structural steel following AWS D1.1
All assemblies and subassemblies should be tested together to guarantee that the final fabrication project works as planned. This should be documented and photographed as part of an organized quality control effort.
Carts and ladders, for example, should be transported in the complete shape feasible. When shipping large fabrications, it is best to include large subassemblies that can be built rapidly on site. The time and money saved by using this unique assembly method are enormous.
Finishing to Add Value
Southern Metal Fabricators can increase the life of a custom metal fabrication and provide a demonstrable return on each project’s investment from surface preparation to final finishing. Our metal storage systems, from oil and gas tanks to feed and grain silos, can withstand harsh outside conditions and maintain the critical substance inside.
The following are examples of decorative techniques:
· Paint or other coating adhesion can be ensured by surface preparation, such as metal bead blasting.
· Custom painting and drying in controlled paint booths to reduce drying periods and ensure the correct hardness of the paint.
· All metal fabrications must be hot-dip galvanized to prevent moisture from weakening their structural integrity.
· Metal powder coating can be used to give intricate railings or metal signage a more beautiful look.
Conclusion:
We provide heavy metal fabrication services following current industry standards and the unique requirements of industrial customers based on our extensive knowledge and a high degree of skill in supplying fabricated solutions. Earth Tech adheres to this metal fabrication life cycle. As a result, we commit to our commercial clients to provide high-quality material handling equipment, answers, and services. To give excellent customer satisfaction, we strive to satisfy the market’s high expectations while maintaining the highest quality standards possible. We aim to please our customers by delivering high-quality items on schedule and making them confident that we meet their material handling requirements.
Latest Posts
Categories
About Our Blog
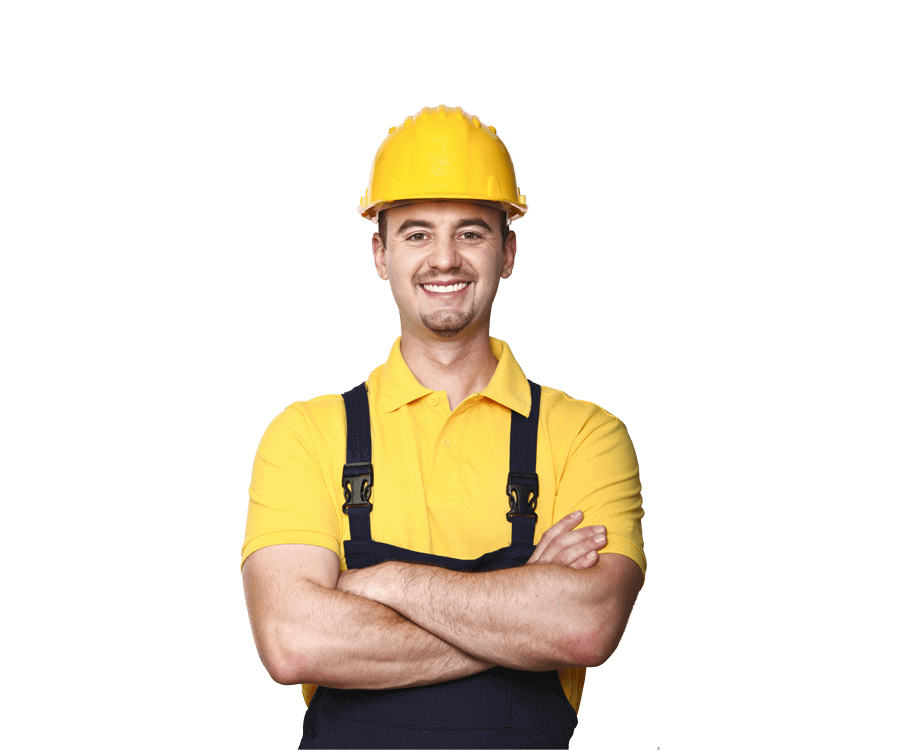
We are so happy you’re here!! Our unforgettable memories in life seem to take place so we decided to Start of Happiness had to be established.