Learn How to Calculate Actual Warehouse Storage Space Area?
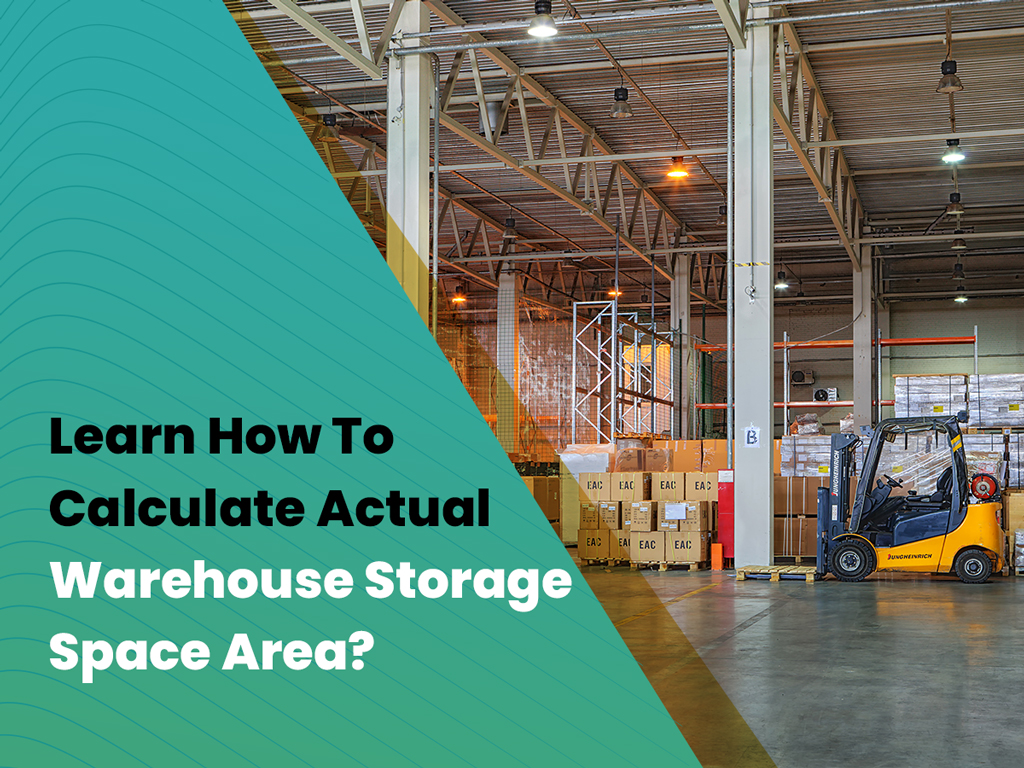
A sprawling space for your warehouse or manufacturing plant can be expensive and difficult to manage. However, if you rent a smaller space, meticulously plan the interiors for storage and maneuvering the equipment. To calculate the storage space, factors to consider include size and type of product, demand and supply requirement and product’s shelf-life, pallets used, workers’ safety, damage prevention, and convenience of handling or lifting items with the forklift. This article shares a few thoughts on calculating the warehouse space, which can prove helpful in your endeavors.
Models for Warehouse Space Utilization:
- 40% space utilization for neatly stacking the products
- 50% space utilization for neatly stacked products with 10-15 times annual turn-around
- 60% space utilization for non-dated coded products, 10-100 SKUs with 10-12 times annual turn-around
- 70% space utilization for non-dated products, 10-100 SKUs with 4-6 times annual turn-around
- 80% space utilization for tightly and neatly stacking products, 1-2 SKUs with no date codes
Important Aspects to Consider when Calculating Warehouse Space
Space is the backbone of storing inventory and equipment in the warehouse. Both over-stacking and under-stacking can prove to be dangerous to employees and can easily damage the products. Hence, its optimal utilization is essential. So, let’s begin with the calculations.
Step#1: Measuring Total Area
From the total area (square feet) subtract the area needed for the cafeteria/canteen, office, and bathrooms. It will provide the precise area available for the warehouse. Now, measure the length and breadth of the area, and the height up to the ceiling. Count the pillars, corners, areas around the duct, fans, lights, and AC units. Based on these measurements, you can consider the quantity, weight, and size of the inventory or equipment for storage. Based on the ceiling’s height and width of the area, you would need to analyze if the inventory should be stowed horizontally or vertically.
Step#2: Measuring Area for Transport
You require a separate area for safely stowing warehouse equipment like ladders and forklifts. A dedicated area should be given to trucks for loading and unloading inventory if you want to safely transport items and avoid accidents in the workplace.
Step#3: Calculating Rack Size
Plan the placement of pallets and racks for properly storing the inventory. Ensure ample space is available between the aisles for hassle-free movement of people and equipment. Further, keep a few racks empty to fill for urgent orders.
Evaluate the legal and safety perspective on the weight, size, and quantity of storage. Additionally, analyze the mandatory free space to be kept on the floor and ceiling. This information you can avail from the state regulatory authority.
Step#4: Scope for restructuring in the warehouse
Consider the entry and exit points including space for water sprays, emergency exits, smoke alarms, and fire extinguishers. Physically inspect the area and click photographs to create a better restructuring blueprint. Once you have the details, feed them into the CAD design software to obtain a 3-D layout design. Ensure you have the calculations for the size of the equipment or container to be stored on the shelf to obtain precise measurements.
With restructuring scope, you will have a better-organized warehouse with greater storage capacity and optimal space utilization, always.
Implementation of Space Calculation in Process Optimization
The total warehouse storage should be capped at 27% to allow the restructuring of the space for new products. If you receive seasonal products like beach or winter gear and holiday decorations ensure that total storage utilization is kept at the bare minimum. Why? It’s because during the holiday season new products are launched and the need to stack those products gets high on the priority list, which leaves the facility overloaded with stocks.
Hence, calculating the space utilization twice a year is ideal, if you seek to boost the business efficiency and growth.
Benefits
Estimating warehouse space offers several advantages. For instance, with an optimal tracking system, you keep a check on the shelf-life of items and can remove them upon their expiry, if not sold. Further, you know the in-demand items and their shipping frequency, hence you can store the exact quantity on the shelves when you know the space calculations.
When you know how much space is available for which types of products, with proper planning you can use several customized storage options from wooden racks, and coil racks to metal pallets.
Conclusion:
A well-organized warehouse storage space boosts productivity and prevents delays in shipping out orders. Further, with safety protocols in place damage to inventory and accidents in the workplace can be significantly reduced.
Latest Posts
Categories
About Our Blog
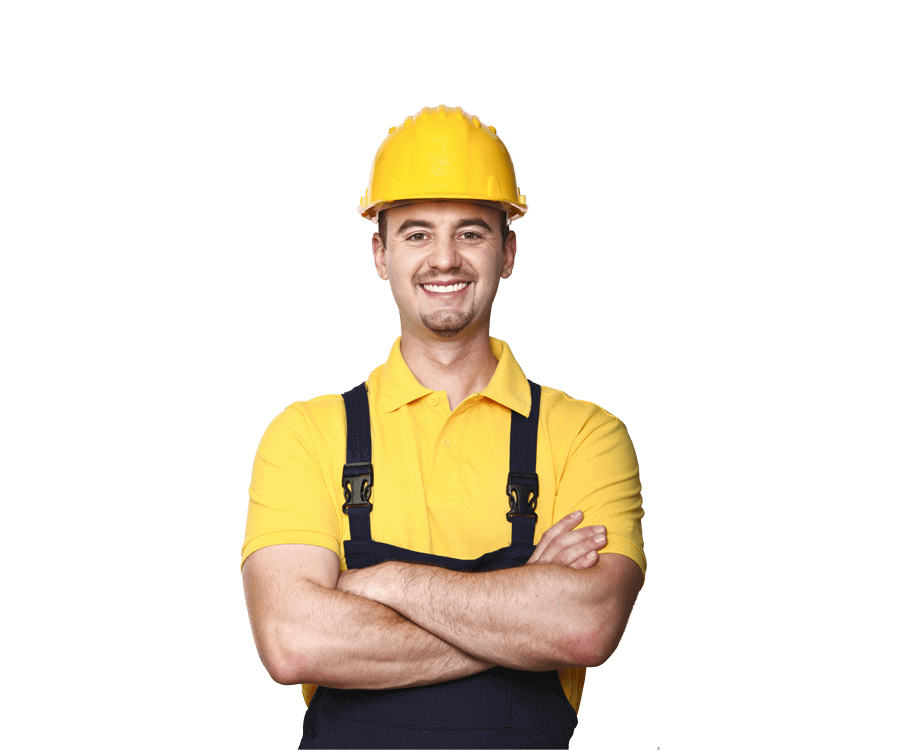
We are so happy you’re here!! Our unforgettable memories in life seem to take place so we decided to Start of Happiness had to be established.