What are Conveyor Systems & How It can be Beneficial to Warehouses?
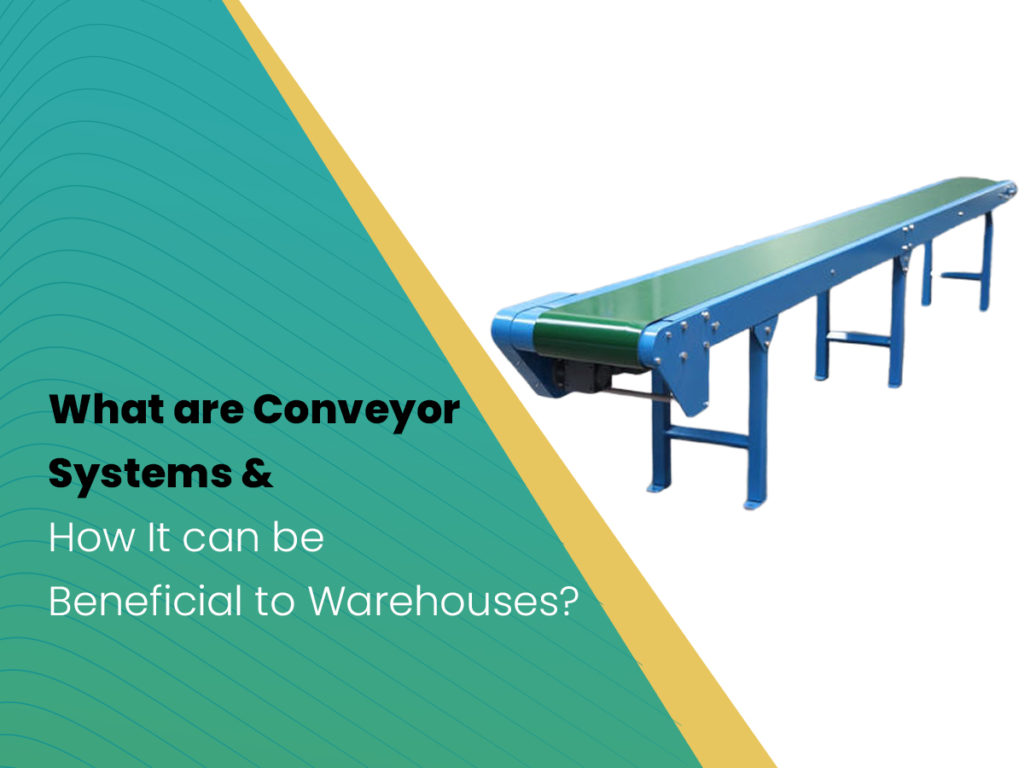
What is a Conveyor System and how does it work?
These days, the conveyor systems are being used in both commercial and civil sectors. The demand of conveyor systems has increased over the years since the industrial and civil sectors have noticed a sharp increase in productivity with installation of conveyor system.
The conveyor system manufacturing companies are estimated to have the CAGR (Compound Annual Growth Rate) at 4.5% within a period of 2020-2025 and are believed to achieve $10.07 billion by 2025.
This is a mechanical handling apparatus which is used for speedy conveyance of different types of products. In a conveyor system:
- A belt remains stretched across two or more pulleys.
- It forms a closed loop around the pulleys to ensure continuous rotation.
- A rotor is used to transmit power to the belt and drive pulley.
- The drive pulley tows the belt and moves the items from one location to another.
The conventional conveyors are straight in shape. However, some conveyors have been designed to bend in different directions in order to deliver the items to the right location. These systems are fitted with cone-shaped rotors or wheels to follow a bend without any difficulty.
Types of Conveyor Systems:
1. Roller Surge Conveyor
There are different types of roller conveyors:
- In a gravity roller conveyor system, a rolling surface is formed by a series of rollers that are attached to the side frame. The products slide down the surface after being placed on the decline angle. The users have to control the speed and the angle of placing the articles on a conveyor in order to prevent collision during transfer.
- A CDLR (Chain Driven Live Roller) system is a combination of chain and gravity conveyor. This type of conveyor is fitted with a gearbox and motor. The rollers are attached to the chain. This mechanism is used in floor mounted conveyors to move heavy materials (pallets, containers, seats, tires etc.). The articles remain still whilst being moved by the rollers.
- In motorized roller conveyors, the rollers are fitted with technologically advance motors. One conveyor system may be fitted with more than one motor to drive the rollers per zone which creates a series of zones along the conveyor belt. Reinforced belts are used to connect the motorized rollers to non-motorized rollers.
2. Feed Conveyor
The feed conveyors are developed by Material Handling Equipment Manufacturer to move raw materials in bulk. These machines are used to:
- Transfer dried animal food products.
- Shred or clean raw materials at the preliminary stage of manufacturing various products.
The feed conveyor functions in the following manner:
- The conveyor is placed close to a vehicle that supplies raw materials.
- The raw materials pass through a valve (fitted to the conveyor) and are collected into a bin.
- The materials are transferred to a storage tank or to a specified point of delivery.
Some feed conveyor systems are fitted with a magnet to separate the ferrous and non-ferrous materials. They can be used to separate the metal debris from the recycled paper. Different types of feed conveyors use different types of transfer mechanisms, such as:
- A rubber belt reinforced with fiber or metal.
- A series of trays to pick up and carry the raw materials vertically to a higher level.
- A sticky artificial or natural rubber belt.
- A curved metal track welded to the central shaft.
3. Belt Conveyor
A belt conveyor is the simplest form of conveyor system that is fitted with a moving belt. It rests on a steel frame which provides support to the belt as well as the articles being transferred. This type of conveyor system can work at variable speed limits due to being fitted with a speed drive.
- In a sliding style belt-conveyor system, a supporting frame is present underneath the system.
- In a conveyor system fitted with roller belt, there are closely placed rollers to provide additional support to the belt.
Implementation of Conveyor in Warehouse:
A conveyor system is designed to quickly and efficiently transfer numerous articles from one part of a warehouse to another or to transfer large and heavy articles. It can be designed to span multiple levels of a warehouse and can be used to transfer articles up and down the floors. Each conveyor system is fitted with an inclined belt to safely unload the articles.
Thus, a conveyor system increases the productivity of a business alongside improving the efficiency of the workers and preventing accidents or injuries resulting from carrying or unloading the bulky or large articles.
Benefits of Having a Conveyor System:
Reduce Time Consumption:
The primary objective of using a conveyor system is to quickly transfer the articles from one part of a business facility to another. It can transfer the goods to different levels or directions of a business facility.
Accidents Decrease
A conveyor system makes the work environment safe for workers since there is no need to manually transfer or unload the heavy or large articles. Therefore, the possibility of accidents reduces when conveyor systems are being used at a warehouse or any other business facility.
Increased Productivity
A conveyor system can swiftly transfer the articles to different levels of a warehouse or business facility alongside being able to transport the goods to different directions. Thus, the productivity of a business as well as the efficiency of its employees increase when a conveyor system is being used.
How to Choose the Right Conveyor System?
You will notice the following issues if you cannot select the right type of conveyor system for a warehouse or business facility.
- Reduced operational efficiency
- Increased operational expenditures
- Customer dissatisfaction
Therefore, it is important to select the right type of conveyor system if you want to provide your business with competitive advantage and have to consider the following factors.
Product requirements
The selection of a conveyor system primarily depends upon the type of the product being transferred and you have to consider the following factors to determine the design and configuration requirements of a system.
- Type of product
- Product’s average weight per foot
- Product’s maximum weight
- Products minimum, maximum and average dimensions
- Each product’s dimensional data
Process requirements
The following factors determine how a conveyor system operates and condition of a work environment.
- Distance between the functional areas
- Features of the pathway (presence of or number of stops, curves, diversions or elevation changes)
- How products will be positioned
- Speed of transfer (rapid/short/slow/steady)
- Availability of space
Transfer Requirements
Different types of conveyor systems are fitted with different types of transfers, such as powered transfers, side transfers, dead plates, gravity rollers etc. The conveyors with powered transfer are suitable for smaller products and conveyors with gravity rollers are suitable for longer or larger products. Thus, it is important to think about the type of the transfer before selecting a conveyor system.
Flow Rate
It is important to select a conveyor system which is capable of handling the average transfer rate as well as the peak seasonal demands of a business facility. The speed and length of a conveyor system depends upon the number of products being transported per hour.
A conveyor system is used to move different types of products within a business facility. There is less possibility of accident and less requirement of manpower when a conveyor system is used in order to transfer the loads. You will notice increase in productivity and efficiency of workers alongside noticing reduction in labor costs if you install a conveyor system at your business facility.
Latest Posts
Categories
About Our Blog
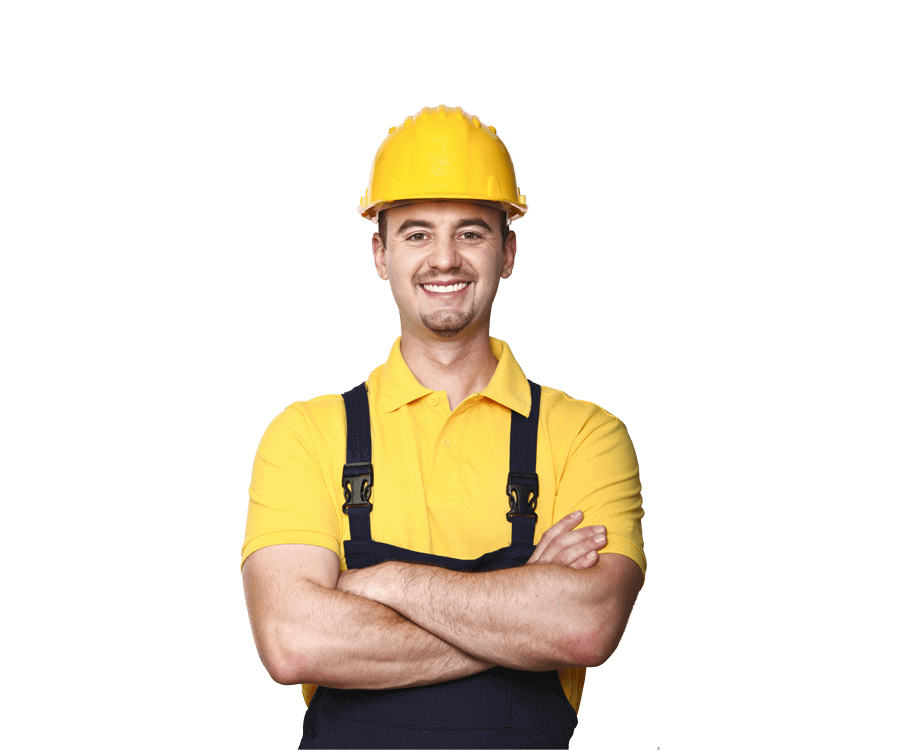
We are so happy you’re here!! Our unforgettable memories in life seem to take place so we decided to Start of Happiness had to be established.