What Are Most Reliable Metal Fabrication Techniques?
Metal Fabrication Techniques:
The difference between a custom fabricated solution and a standard meta fabrication can be told in one word by a full-service fabricator; value.
Every custom metal fabrication starts with research to access the proper material and methods to cost-effective produced specific fabrication design. From small metal accessories to massive steel silos, the custom metal fabrication process is crafted to create more versatile, good-quality results that provide long-term value, from design to delivery.
Creating metal parts contains various kinds of methods of metal artifices. The picking of processes depends on the required end result as well as the type of metal, its shape, etc.
Sheet metal fabrication and metal fabrication are the two categories of fabrication based on shape. While the initial excludes CNC machining the latter includes all fabrication techniques.
The list of the metal fabrication processes is extremely lengthy as it contains a number of surface finishing operations, cutting, machining, etc. Still, we can claim that there are few selective ones that rule over others as the most widely spread techniques.
Here are some examples of custom fabrication techniques that create quality fabrications with extended-term value.
Setting Design Intent
The metal fabrication design is crucial to outreaching the aspired outcome, which is desired value. The most asked question in the niche is: What is the aim of the fabrication? Maybe it is an industrial solution to give a roof way in for two oil tanks with multiple entry points? Or perhaps there is a unique bulk storage design that calls for multiple custom components, such as a fully-insulated skirt with ground access?
A full-service fabricator is able to take a standard industrial plan or an engineering drawing to push out a detailed design that will execute the desired output for even the most complicated fabrication. This might need refining and testing the design as per industrial-specific needs and recognizing all the needed parts to serve as the foundation for the final project.
This process is perfect for custom meta fabrication such as:
- Dry solids include hoppers, grain tanks, feed, silos, and other material handling functionality.
- The capability of heating syrup up to keep it in liquid form, Liquid feed handling with quality control ability.
- Access to storage units of different heights along with custom wrap-around spiral staircases with cross-over platforms.
Custom fabrication may start with MTC shape cutting, AutoCad files, Pro Nest, or even an old-fashioned hand-drawn plan. But with the correct engineering expertise, the design can be made sure that the projects connect with every value-add specification – before the actual fabrication starts.
Metal Cutting & Forming
Before the cutting starts, the metal fabricator must access what kind of method is suitable for metal kind and thickness. Laser cutting exertion is effective for heavy steel plates that require strict tolerances or delicate fabrications. Lasers are not suitable for metal materials or composites that are not pure, due to potential surface defects or risk of spray reactions.
When the fabrication needs complicated steel metal shapes, plasma devices with Computer Numeric Control (CNC) can offer exceptional accuracy. Plasma tables are usually utilized for sculpting circular holes or complicated shapes out of thick metal plates.
Sawing is more suitable for structural steel projects that need large beams to serve as the foundation for the fabrication output. In order to cut easy shapes, plate shears are the most cost-driven option, which is more suitable for carbon steel ductwork or durable metal bins.
Establishing the metal might need bending, angle and plate rolling, or punching. It is important to pick the correct devices to deliver the desired output.
The metal forming device might include:
- Mechanical and CNC hydraulic press brakes.
- Plate rolling and angle rolling machines.
- Beam punches and CNC punching machines.
- Multi-function ironworkers for sheering, punching, and bending.
Custom Welding & Assembling
Custom welding and assembly methods can make sure that each metal fabrication is meeting specific industry standards. A custom fabricator with certified welders and a documented quality control program (QC) is more likely to satisfy industry needs that add worth.
Before partnering with a metal fabricator, ask for documentation of welder certifications. These credentials should enclose:
- Adherence to Canadian Welding Bureau (CWB) standards.
- Welding Procedure Specification (WPS) that conforms to ASME Section 9 and welding practices that conform to the API-650 standard.
- Qualified to weld structural steel according to the American Welding Society AWS D1.1.
All groups and subgroups should be sampled jointly to guarantee final fabrication project functions as planned. The whole pack process should be photographed and documented as part of a structured QC program.
The fabrication pieces should be exported in the most comprehensive state possible, particularly for carts or ladders. Larger fabrications should be exported with large subgroups that can be built rapidly on spot. This custom assembly procedure can dramatically decrease project timelines and toil fees.
Finishing to Add Value
From exterior preparation to final output, Southern Metal Fabricators can extend the life of a custom metal fabrication for a tangible return on each project investment. From oil and gas tanks to feed and grain silos, metal storage services can persist in punishing outdoor conditions and protect the valuable content inside.
These finishing methods include:
- Metal bead blasting or other surface prep to gurantee paint or other coating adheres to the metal’s surface.
- Custom painting and drying with controlled paint booths to expedite dry times and proper hardening.
- Hot-dip is galvanizing to coat every nook and cranny of the metal fabrication to prevent moisture from compromising structural integrity.
- Metal powder coating for more decorative finishing on detailed railings or metal signage.
From design to delivery, Earth Tech proffers finishing methods like these and other fabrication services that decrease project toil costs and increase product ROI.
Latest Posts
Categories
About Our Blog
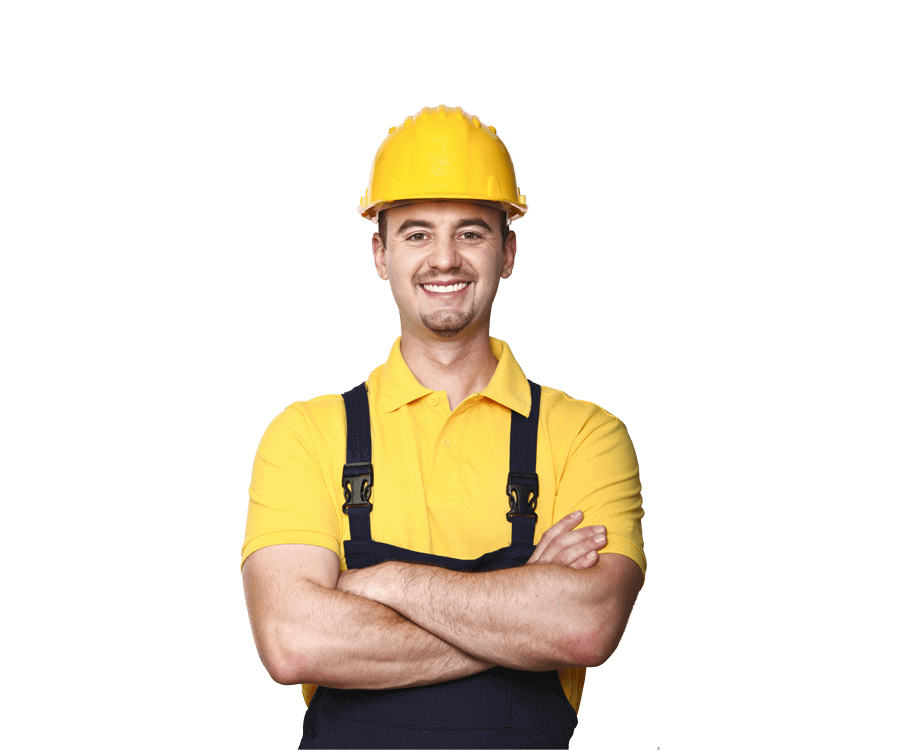
We are so happy you’re here!! Our unforgettable memories in life seem to take place so we decided to Start of Happiness had to be established.