Which Welding Type is Best in Engineering Fabrication?
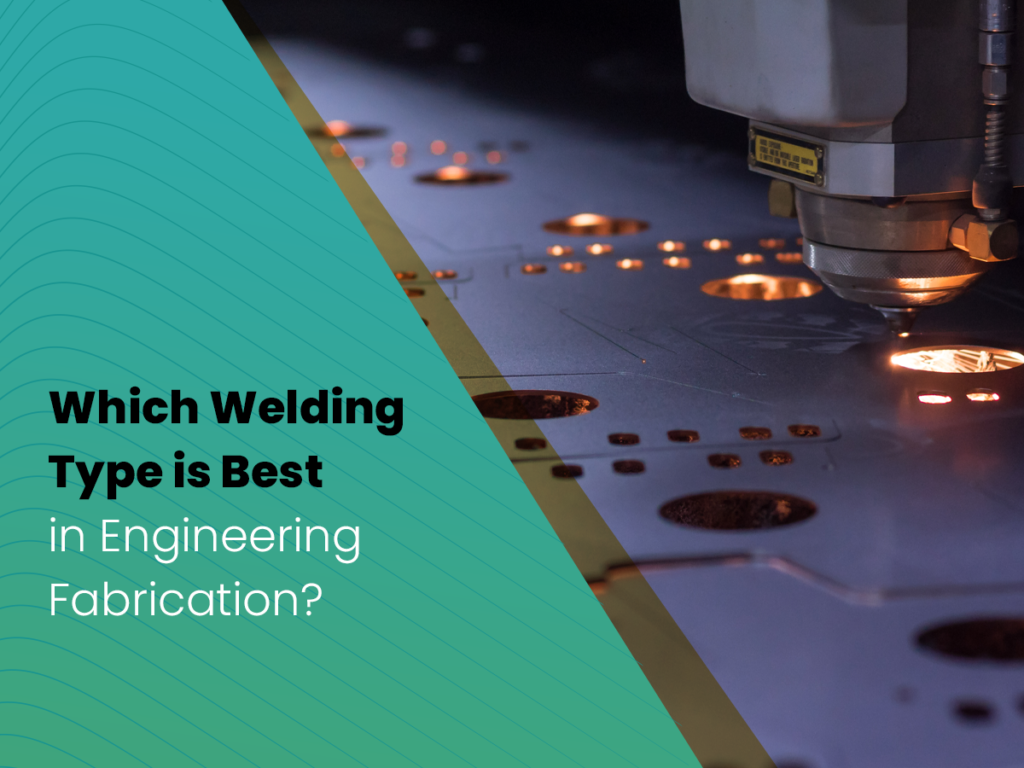
What is Metal Fabrication?
Metal fabrication is the process of manufacturing sheet metal and various other metal parts or structures from raw metal. There are different types of engineering fabrication techniques, such as bending, cutting, welding and punching. The fabrication process starts with a sheet of metal. The thickness of this metal sheet may be one quarter of an inch or less. The metal sheets are pliable at this thickness and can be shaped via cutting, folding, stamping or welding.
It is possible to combine multiple metal fabrication techniques to manufacture custom metal structures. Metal fabricators are trained experts capable of skillfully manipulating the metal sheets in desired shapes and metal fabrication is carried out at manufacturing plants or fabrication shops. The metal components being used in the medical industry or IT industry require specialized fabrication service.
Metal Fabrication Stages:
The process of sheet metal fabrication varies from one project to another. However, the following stages are present during the majority of the metal fabrication proceedings.
Designing:
The designing process is completed in different ways by different companies. However, many sheet metal fabricators consult with the clients to collect specifications before starting a project of metal fabrication. The designing team and production team work with the client in this scenario. An experienced designer who knows CAD (computer aided designing) assists in designing to ensure that the final product has been properly designed. At this phase, the designing team works with the client in order to determine requirements of a project, different manufacturing approaches and different areas of improvement.
Programming:
The CAD design is translated into programming for a computer-controlled machine once it has been finalized. This programming is used for automated punching, cutting and turning of machines. The metal parts are drawn and imprinted upon a metal sheet in 2D form which ensures proper utilization of the material.
Cutting:
Concentrated LASER beam is used for cutting the sheet metal. It cuts through the metal sheet according to the programming and can accurately cut through the sheet based upon the programmed design.
Punching & Bending:
A CNC punching machine is used in some scenarios to perforate the metal sheets during fabrication. Different types of perforations, such as louvers, ribs, countersinks etc., are created through punching. The CNC punching machines are used for this particular task. These machines use various tools for shaping or perforation of metal sheets according to the programming.
A CNC folding machine is used for bending of metal sheets. Different types of machines, such as automatic panel bending device, manual press brake or robotic bending cell, are used for this task. The type of the machine that is used for bending depends upon the size of the metal part or complexity of the task. These devices apply pressure to mould the metal sheets in a specified curvature.
Welding:
Different types of welding techniques are used for metal-sheet fabrication, such as TIG, MIG, spot, projection or robotic welding.
Assembly:
The metal parts are assembled in different ways. For example, they may be assembled through welding or with the help of electrical integration using a wire harness along with PAT testing and hardware installation. The process of assembling different parts depends upon the features of the final product.
It may become necessary to press nuts, studs or other components when assembling the metal parts. This process is known as insertion which is performed in order to fasten the product together.
Powder Coating:
In this process, electrostatically charged powdered particles are sprayed onto the metal surface. The powder-coated surface is cured using a specially designed machine. The coating sticks to the surface after curing and provides the metal substrate with a protective layer.
Types of Welding Techniques:
TIG WELDING:
The TIG (Tungsten Inert Gas) welding technique is commonly used in order to fuse two pieces of metal together with application of extreme heat. In this method, tungsten electrodes deliver electrical current to the welding arc. The extreme heat generated by the electrical current melts the metal parts leading to fusion. This welding technique is ideal for thin materials due to low heat input.
The continuous flow of an inert gas, such as argon, shields the welded area and tungsten electrodes from the air enabling the metal parts to fuse together. The argon gas is mixed with hydrogen, helium or nitrogen in some scenarios depending upon the needs of a project. The single-sided spot-welding method is used sometimes. It prevents oxidation and resists corrosion.
SPOT WELDING:
The ‘spot’ welding method is also known as resistance welding. The resistance welding machines are equally useful for large and small projects. In this welding technique, electrical current is used in order to generate heat and to seal the frayed edges of the metal. This technique is suitable for welding the metals with low melting points since it causes no distortion.
MIG WELDING:
This is a semi-automatic process of welding which results in firm joining of two pieces of stainless steel. The argon gas is used during the process along with solid wire electrodes. It is possible to use pulsed electrical current during MIG welding. Thus, it becomes easier for a professional to weld the spots that are hard to reach during complex fabrication projects.
The welding gun maintains a continuous flow of consumable electrodes during MIG (Metal Inert Gas) welding. It creates an electric arc between a piece of metal and the wire. The metal pieces melt and become fused due to the extreme heat generated by this arc. The argon gas shields the area, which is being welded, from air to ensure proper fusion. The argon gas may be mixed with carbon-dioxide, oxygen or helium to improve the quality of welding by stabilizing the arc.
Metal fabrication is a complex process. It can be performed by trained fabricators who have extensive knowledge in this field, access to the right set of tools and machines and stay updated about the latest developments in this field. Experienced metal fabricators can provide customized service to their clients based upon each project. They can help businesses reduce material expenses and manufacturing cost whilst identifying the right technique of fabrication and welding depending upon the type of metal or uniqueness of different projects.
Latest Posts
Categories
About Our Blog
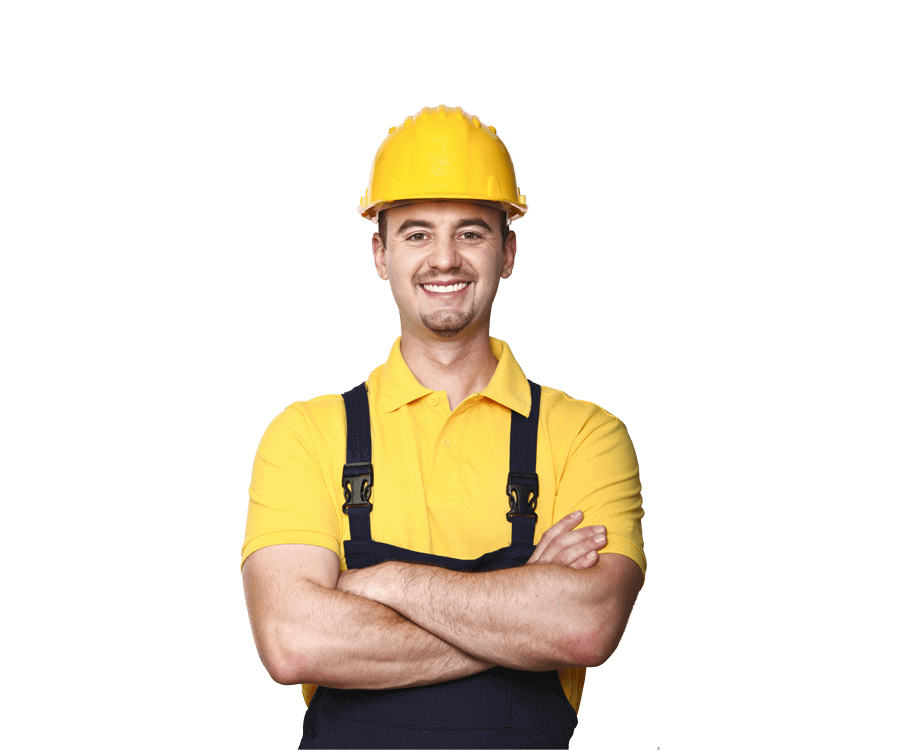
We are so happy you’re here!! Our unforgettable memories in life seem to take place so we decided to Start of Happiness had to be established.